プラスチック射出成形品のスプルー・ランナー・ゲート
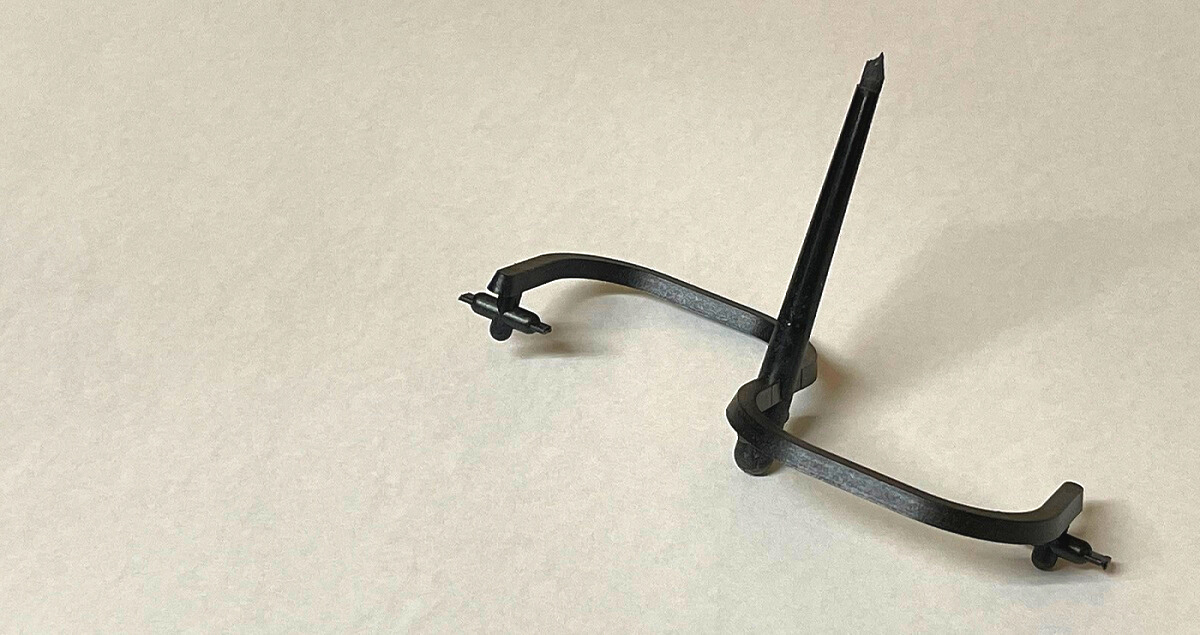
熱可塑性プラスチックの成形法の一つである「射出成形」では、成形機のノズルから溶融樹脂を金型に射出して成形します。
金型には射出された樹脂が通る通路があるのですが、それが「スプルー・ランナー・ゲート」です。
1、スプルー・ランナー・ゲート
射出された溶融樹脂が最初に流れる金型流路をスプルーと呼び、分岐路のことをランナー、キャビティへの入り口をゲートと呼びます。(図1)
キャビティとは、樹脂が流れ込む金型の凹型のことです。
この「スプルー・ランナー・ゲート」の寸法・形状・位置によって、成形品の品質やコストが大きく左右されるため、金型設計の段階で十分な検討が必要となります。
2、ランナー方式
コールドランナーは、成形品とともに本来は不要であるスプルーやランナーが生産される方式です。
ホットランナーと比較すると、金型費用が低く、納期も短いという利点がありますが、成形サイクルが長くなる、ランナーを再利用するために粉砕する手間や設備が増えるなどの課題もあります。
ホットランナーは、スプルーやランナーを常に溶融状態に保ち、成形品だけを生産できる効率のよいランナー方式です。
コールドランナーと比較すると、生産効率が高く、超多数個取りも可能という利点がありますが、金型費用が高く、納期は長い、金型メンテナンスが難しいなどの課題もあります。
3、ランナーレイアウト
射出成形品の取り数は、1個取り→2個取り→4個取り→8個取り→16個取りのように2ⁿ個に設定するのが基本です。
取り数を検討する場合、スプルーから各キャビティまでのランナー長さが等しい「等長ランナー」であれば、4個取りまでは各キャビティへの溶融樹脂の充填が均一であり、品質バラツキを最小限に抑えることができます。
したがって、寸法や形状精度の厳しい精密成形における取り数は、4個取りを限度とするのがよいでしょう。
4、ゲート方式
シール機能とは、キャビティに充填された溶融樹脂が成形機側に逆流しないようゲート部が固化し、シールする働き。
発熱機能とは、ゲート部において圧力損失が増大し、そのエネルギーが熱に変化して樹脂温度を上昇させる働き。
制流機能とは、溶融樹脂の流動方向や流量などをコントロールする働き。
ゲートの種類には以下のようなものがあります。
①ダイレクトゲート
別名スプルーゲートとも呼ばれ、スプルーをそのままゲートとしたものです。(図4)
取り数は1個に限定されますが、ゲート部で流路が絞られていないので圧力損失が小さく、大型深物成形に向いたゲート方式です。
②サイドゲート
成形品の側面にゲートを設ける方式で、ゲート部の加工が簡単で多数個取りにも対応できることから最も一般的に使用されています。(図5)
③オーバーラップゲート
サイドゲートがPL面に近い成形品側面にゲートを設けるのに対して、オーバーラップゲートは成形品と反対側の金型にゲートを設けます。つまり、PL面から溶融樹脂がキャビティに流入する形になります。
④ファンゲート
ゲート開口部は薄く幅広ですが、ゲートランド部はランナー部まで徐々に勾配をつける形状がよく用いられます。
この方式はジェッティングが生じにくく、フローマークなどの成形不良防止に効果があります。
⑤フィルムゲート
ファンゲートよりもさらにゲート幅を広げ、厚さを薄くしたゲート方式です。(図6)
矩形の平板状成形品などに用いられ、そりや歪みの少ない成形品を得ることができます。
⑥ディスクゲート
フィルムゲートを、中央部に丸い穴のある成形品に適用したもの。(図7-a)
この方式は、射出された溶融樹脂が中央部から外側に放射状に流れるので、キャビティ内のエアーが抜けやすく、ウェルドラインを生じない利点があります。
⑦リングゲート
丸い小型成形品の外周部PL面に設けるリング状のゲートです。(図7-b)
ディスクゲートとは逆に外側から中央部に溶融樹脂を充填させます。
全周から同時に充填させるので円筒度のよい成形品が得られる反面、中央部に穴のないキャップ状成形品の場合は、ショートショットやヒケおよび焼けなどの成形不良が発生しやすくなります。
⑧タブゲート
成形品にタブと呼ばれる余肉を設け、そのタブにサイドゲートを設ける方式です。
タブを設ける理由は、ゲート付近に残りやすい内部歪をタブで吸収することにあります。
⑨サブマリンゲート
トンネルゲートとも呼ばれ、金型構造によって自動的にゲートが切断されるゲート方式です。(図8-a、b)
⑩カシューゲート
成形品の上面にゲート跡が許されない場合、このゲート方式を用いれば直接コア側にゲートを設けることができます。(図8-c)
⑪ピンポイントゲート
3プレート構造で自動的にゲートが切断されるゲート方式であり、略してピンゲートと呼ばれます。(図9)
ランナーレイアウトの自由度が高く、小さな成形品から大きな成形品まで応用性の高いゲート方式です。