射出成形の工程
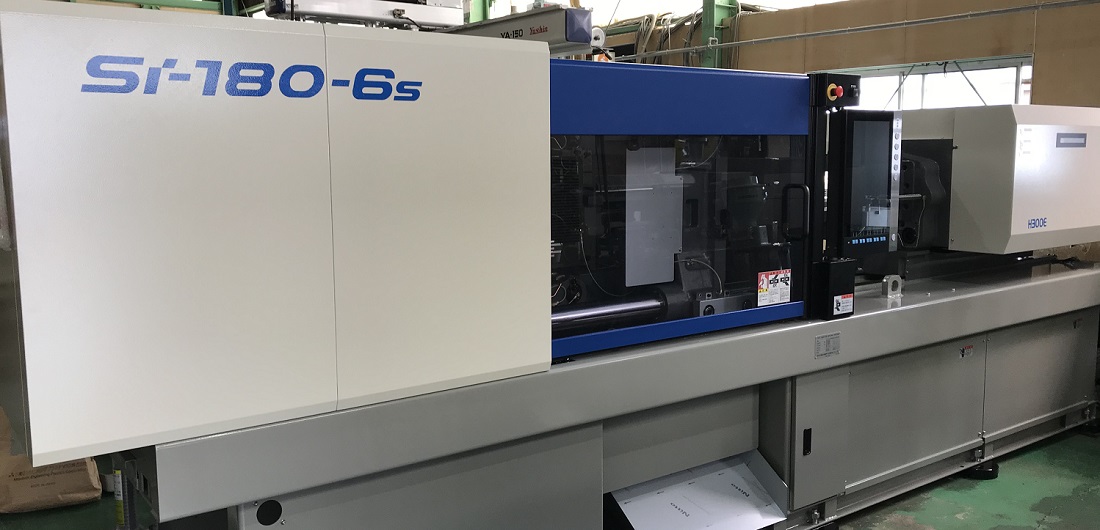
プラスチック製品を作り出す「射出成形」(インジェクション成形)とはどのようなものなのか?
どんな機械を使い、どのような工程によって大量生産を行っているのか?
今回はそのような疑問に答えるために、「射出成形機の構成」と「射出成形の工程」について解説します。
1、射出成形機の構成
射出成形機の基本的な働きは、金型を開閉し、樹脂を溶かし、樹脂を金型内に射出することです。
そしてこの射出成形機には様々な種類があるのですが、代表的なものに図1のような横形の射出成形機があります。
このタイプは、操作側から見て左側に型締装置、右側に可塑化・射出装置が配置されています。
金型は型締装置に取り付けます。
実際の生産現場では、成形機のほかに以下のような周辺機器が使用されています。
- 材料乾燥供給装置(プラスチック材料を乾燥する)
- 金型温度調節機(金型の温度を一定に保って成形を安定させる)
- 自動取出し機(金型から突き出された製品を自動で取り出す)
- ベルトコンベア(取り出した成形品を次工程に搬送する)
- ゲートカットロボット(成形品のゲートカットを自動で行う)
- 粉砕機(切断されたランナーを粉砕する)
2、射出成形の工程
前述のように成形機は、型締め装置と可塑化・射出装置に分かれています。
そして、可塑化・射出装置では「可塑化(計量)」→「射出」→「保圧」の3工程を繰り返し、型締め装置では「冷却」→「型開き」→「取出し*」→「型締め」の4工程を繰り返します。(図2)
(*突出し工程は取出し工程の中に含んでいます。)
可塑化工程(計量工程)
可塑化工程は、プラスチック材料を溶かすと同時に射出する樹脂量を計量する工程でもあります。
材料がスクリューの回転によりノズル側に送られながら射出シリンダーに巻かれたバンドヒーターと、材料同士の摩擦による発熱によって溶かされます。
この時、金型に射出される樹脂量を毎ショット同じにするためにスクリュー回転数と背圧を制御します。
射出工程
射出工程は、溶けたプラスチック材料を金型に射出注入する工程です。
そのためにスクリューは回転を止め、ノズル側へ前進させることで溶融樹脂を金型内に射出します。
保圧工程
保圧とは「保持圧力」を略した言葉であり、金型に射出注入された溶融樹脂に圧力を加え続けることです。
この保圧は少なくともゲート部が固化するまでかけ続ける必要があります。
そうしないとゲート部から樹脂圧力が抜けてしまい、成形品の収縮量が大きくなってしまって様々な品質不良を引き起こしてしまいます。
冷却工程
射出成形工程において冷却工程とは、保圧工程完了から型開き開始までの時間を言います。
この時、可塑化・射出装置では可塑化(計量)工程が平行して行われています。
成形サイクルに占める冷却工程の割合はとても大きいため、金型設計においては冷却回路設計が非常に重要になります。
取出し工程
取出し方法には、「自然落下」による方法、「取出しロボット」による方法、「手動」 による方法などがあります。
「自然落下」による方法は、取出し時間も短く、簡単なシュートと収納箱で取出し可能なため、外観の問われない小物部品などに多用されます。
「取出しロボット」による方法は、設備投資を必要としますが、成形サイクルが安定するので品質のバラツキが小さくなります。
「手動」 による方法は、設備投資が不要なため少量生産や労務費の安い開発途上国での生産に用いられますが、成形サイクルが安定しないため、品質のバラツキが大きくなりやすい。